In our last blog in this series (Using Viscosity to Understand Fluids for Oil Field Operations), I shared that I would be covering the testing of oil and gas. In my upcoming blogs I am going to cover three points:
1) High Viscosity Friction Reducers (HVFR): Measuring viscosity, break test at downhole conditions, and viscoelastic properties
2) Produced Oil: Simulating the path from formation to surface
3) Motor Oil/Engine Lubricants: Why proper testing is key
Today's blog will be focused on testing high viscosity friction reducers (HVRFs).
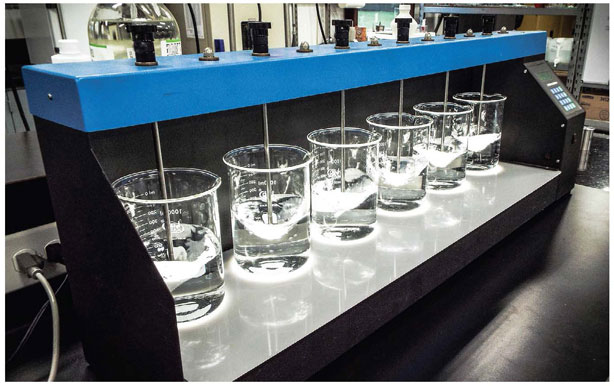
HVFR’s are quickly becoming the new “norm” for frac jobs in North America. FR water (Slickwater) jobs were becoming very popular due to the high pumping rate the systems can be run at, the fracture complexity driven by the high rate and low viscosity fluid, not needing as many hazardous and expensive chemicals on site, and significantly higher regained conductivity of the produced fractures due to MUCH lower residue being left than we see in gel jobs. But these systems had a major issue which was the need to run incredible amounts of fresh water. With a lower viscosity, proppant transport capability is reduced so you had to run more volume at lower proppant concentrations to deliver the same amount of proppant. Produced water is not a viable option for conventional, FR-based fluid systems due to the polymer’s inability to properly hydrate and remain stable in water with high salinity/TDS. Gel-based systems work well in certain formations under specific job design conditions. A large majority of wells in North America are now drilled horizontally through the expected “pay zone,” and jobs are designed to utilize as much of the horizontal length as possible while placing a specific pound of proppant per foot. The goal is to extend fractures as far into the formation as possible with higher complexity allowing for maximum reservoir contact and, in turn, faster and easier oil recovery. The high viscosity of gel systems (~300-500 cP) needed for the desired proppant transport leads to these fluid systems creating shorter, wider fractures with little to no complexity (theoretically a perfect bi-wing fracture). Also, guar gel leaves a significant amount of residue after the fluid is broken due to the makeup of the long-chain polymer and how/where breakers act on the chain. This residue will cover the face of the formation or leach into the permeable pathways in the formation or, more likely, those in between the grains of proppant where they are entrapped and ultimately lead to reduction in regained conductivity. The main goal of a hydraulic frac job is to increase the radial drainage area towards the wellbore so that oil can flow freely to the surface. This is done by increasing permeability by way of adding proppant packs with permeability 10,000 to 100,000+ times that of the formation (down to nanoDarcy levels of permeability in shale formations). Another property that needs to be considered and improved is conductivity. With residue affecting flow through the proppant pack and with the pack being a shorter, high concentration zone, quite a bit of the conductivity that was added to the flow path will be lost. Longer, connected channels of proppant (even at lower concentrations along the path) and extremely low residue (nearly 100% expected flowback) are the optimal conditions for the best possible hydraulic frac job under the constraints of current job designs. This happens to be exactly what HVFR’s provide! Why is that?
HVFR systems are run at FR loadings of 1-10 gpt as opposed to 0.5-1 gpt of conventional FR systems. This higher loading increases the viscosity of the fluid system usually to a high end of ~30-80 cP so you can transport a higher concentration of proppant per gallon of fluid than with low concentration FR systems reducing the water requirements for the job. The viscosity is also low enough that pump rates can remain high (both needed for fracture complexity). Another interesting find is that at higher concentrations, the friction reducer can hydrate more readily and remain stable in water with relatively high levels of TDS which again reduces the need/use of fresh water on each job.
Now where does viscosity factor into this equation? Just like with gel-based systems, you will need to continually, AND ACCURATELY measure the viscosity of the HVFR fluid system to make sure that proper hydration is occurring. Along with this, you can use the viscosity, understanding of the properly hydrated system viscosity values, and downhole pressure responses to make changes to the system “on-the-fly”. Mainly, if conditions are appropriate, you can begin to work the loading of the HVFR down which will ultimately save money and lessen the amount of polymer (polyacrylamide) downhole making it easier to fully break and flowback. Viscosity should can more than just a spot check and instead act as a guide to optimizing the pumping of your fluid system, but it only works if you have proper data and actually use the information. Contact your local RheoSense representative to learn more about this. If you can save a couple thousand or even a couple hundred gallons of FR on a job, one of our instruments would pay for itself very quickly!
While understanding the pumping conditions is extremely important, it is just as important, if not more, to understand what the fluid will do once the pumping for that stage is done. Mainly, how long will it take for the system to fully break. Break tests are currently done either under static conditions in a water bath with visual inspections to determine viscosity or on a rotating system with a heat cup. Both of these methods are poor representation of downhole conditions and therefore don’t provide an accurate indication of what to expect from the fluid once it is downhole. They do not take formation cooling into effect and simply test at original bottomhole temperature. Breaking usually occurs quickly due to certain breakers being temperature activated. With a RheoSense viscometer, you could program in a temperature sweep to simulate the wellbore heating back up after being cooled by the surface temperature frac fluid. You can also program the system to wait “x” amount of time so that the sample sits at the desired temperature for the amount of time that you desire prior to taking a measurement. This means that you no longer have to sit by your viscometer and log data and tweak the settings. You can set your measurement protocol (for the temperature sweep), load the sample, and go do other work. Our system stores the data and it will be ready for you when you get back to it. Adding a RheoSense viscometer to your lab actually makes your job easier…what more can you ask for!
I want to cover one final viscosity test for HVFR systems. This is not a conventional viscosity measurement, but it is one that is proving extremely important for this type of system. It also has uses or potential uses to aid in better understanding other properties of HVFR and other fluid systems relating mostly to various fluid mechanics and fluid delivery. Without this, we probably would not understand how HVFR systems transport and suspend proppant at the concentrations that they do. Originally, it was thought that while HVFR loadings increased viscosity to a point, the increase would not be enough to allow for proper transport of desired proppant concentrations. Gel carries and suspends proppant due to its viscosity which is in the 100’s of centipoise, but once the fluid came to rest (or flow was slowed significantly similar to what happens when the fluid enters a fracture….Fluid goes from shear of ~500 1/sec to somewhere between 10 – 100 1/sec) proppant began falling out and was fully settled quite quickly. This made the prospect of running your gel loading too low very unnerving since that could lead to early sand settling and in turn could possibly cause a screenout.
So why would a fluid with a MUCH higher viscosity not have greater proppant transport under low shear conditions? This can be explained by viscoelastic properties of each. While gel systems tend to have lower elasticity, HVFR fluids are highly viscoelastic. Basically, even under no shear conditions, these fluids will work to maintain their shape/form so they maintain the ability to suspend proppant longer than the gel-based systems even though the gel system has a viscosity 10 times greater than the HVFR system. This property can also help define how chemical additives act once inside of the fracture under low-shear conditions. Which could help answer questions like: How far do surfactants travel into the fracture? Are they spent right at the first contact with the rock face or do they travel with the frac fluid and disperse gradually? And quite a bit more can be learned by understanding the viscoelastic properties of a fluid or fluid system.
This testing is relatively new, but RheoSense has the e-VROC® viscometer (or VROC initium one plus) for extensional viscosity testing. The data you gather from this testing can be used to understand or define a variety of fluid properties that can be very important as you can see from the work with HVFR systems. With the extensional data that our instrument measures, you will be able to obtain normal stresses and relaxation time for samples. These values will show how elastic the samples are. Finally, with data gathered with our instruments, you can calculate the Weissenberg number for your sample which indicates elastic to viscous forces. At this point, you have all of the data you need to truly understand how your fluid system should be expected to carry and suspend proppant...but only at no shear and room temperature conditions.
Want to learn more about viscosity of HVFR systems? Join us on Monday, January 23rd as we are joined by oil and gas expert Carl After for a discussion of live discussion of factors effecting viscosity measurements for friction reducers and a presentation of viscosity data for low concentration polyacrylamide formulations.
Or contact us if you have any questions about extensional viscosity testing or to discuss specific testing questions with one of our experts!
Obtaining the elastic properties of your samples as described above provides a major piece of the fluid dynamics puzzle that we are interested in, but to FULLY characterize your samples and truly understand all of your options you will need to go one step further with a thermal stability study. This simply means you will need to get viscosity values for your samples across a range of temperatures (such as your expected cool down temperature or the fluid temperature on surface up to your expected maximum bottomhole temperature). By measuring viscosity at multiple points in between the temperature minimum and maximum, you will be able to see the trends the sample is following. While you should almost always expect the viscosity of polymers to decrease with increasing temperature, understanding the rate at which the viscosity decreases is extremely important. Plus, you may find that the viscosity some samples begin declining more slowly or stop declining at all at certain temperatures. It would be best to run this thermal stability study at multiple shear rates as well. It should be sufficient to run one at ~511 1/sec and one somewhere between 10-70 1/sec. Why should you do this? It will provide thermal stability information both during pumping and traveling through the wellbore (high shear) as well as during the time in the fracture (low shear). With that, you now have all of the data necessary to compare various fluid systems and CONFIDENTLY determine the best and/or most cost-effective option for your job. You are now armed with the knowledge of what the fluid is doing downhole depending on the conditions at that time. If you need to shut down pumping during a sand stage, would be well-equipped to determine if it would be possible to resume pumping likely without issue or if it is likely that proppant has fallen out and settled where a near wellbore screenout would be probable.
A thermal stability study may be difficult or take an excessive amount of time with other viscometers, but with your RheoSense instrument, setting up and running a full thermal stability study is incredibly easy and fast (likely only requires one sample to run the study!). You will just need to type in the temperatures you want to test at in the temperature sweep tab and click RUN. Our instruments do the leg work so you can focus on the job and other tasks at hand.
Stay tuned for my next blog post as I dive into Produced Oil: Simulating the path from formation to surface.
Written by: Tyler Etheredge, RheoSense Technical Sales Specialist
COMMENTS